
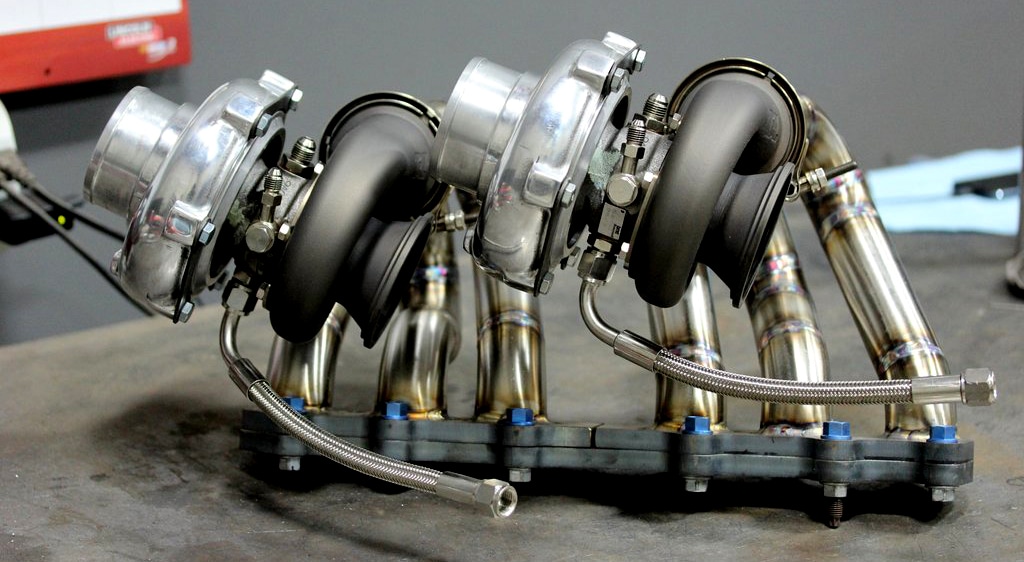
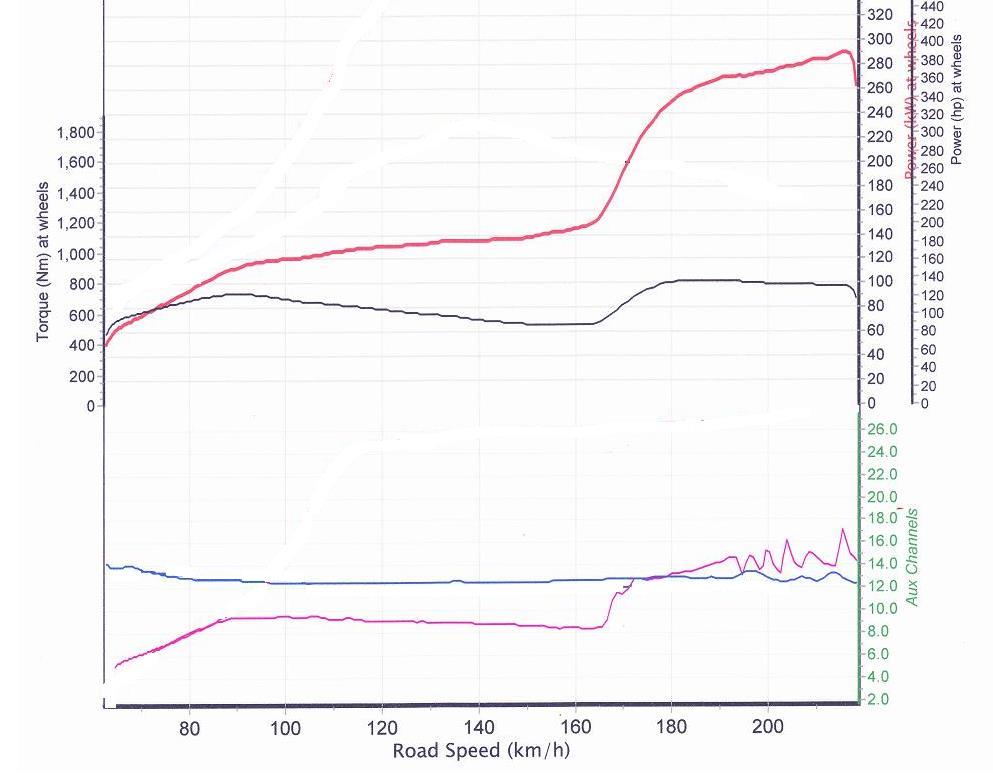
Two Stage serial sequential systems offer car makers flexibility in leveraging the fuel efficiency benefits of engine downsizing or delivering performance upgrade to an existing engine platform. The latter thus continues in mono mode, optimizing fuel efficiency and performance at higher engine speeds. At this speed, both the turbine and compressor by-pass valves are fully open, regulating the gas flow only to the larger LP turbo. Beyond 1500rpm, the turbos continue to work together, but the turbine by-pass valve progressively channels more exhaust gas to the low pressure turbo until full transition takes place, usually around 2,800rpm. This provides a rapid ramp-up of boost pressure and contributes to enhanced torque and responsiveness. At low-speed – up to about 1500rpm – the two turbos work in full serial mode, with the compressor and turbine by-pass valves closed. The gas flow between the turbos is controlled using by-pass valves whose operation modes are based on the engine speed. In a Two Stage Serial system, a small high pressure turbo (HP) works together with a larger low pressure turbo (LP). Two Stage Serial sequential systems are typically specified for diesel engines in the 1.6L to 3.0L range, although the bulk of their adoption is for the 2.0L segment where the effect of engine downsizing or power uprating is more pronounced. This Two Stage configuration is chosen by auto manufacturers either to deliver engine downsizing or to uprate performance. Garrett’s Two Stage Serial sequential system is the ideal turbo architecture for powertrains where ultimate power density and part-load emissions are primary considerations.
